Effective Ways to Use a Torque Wrench: Essential Tips for 2025
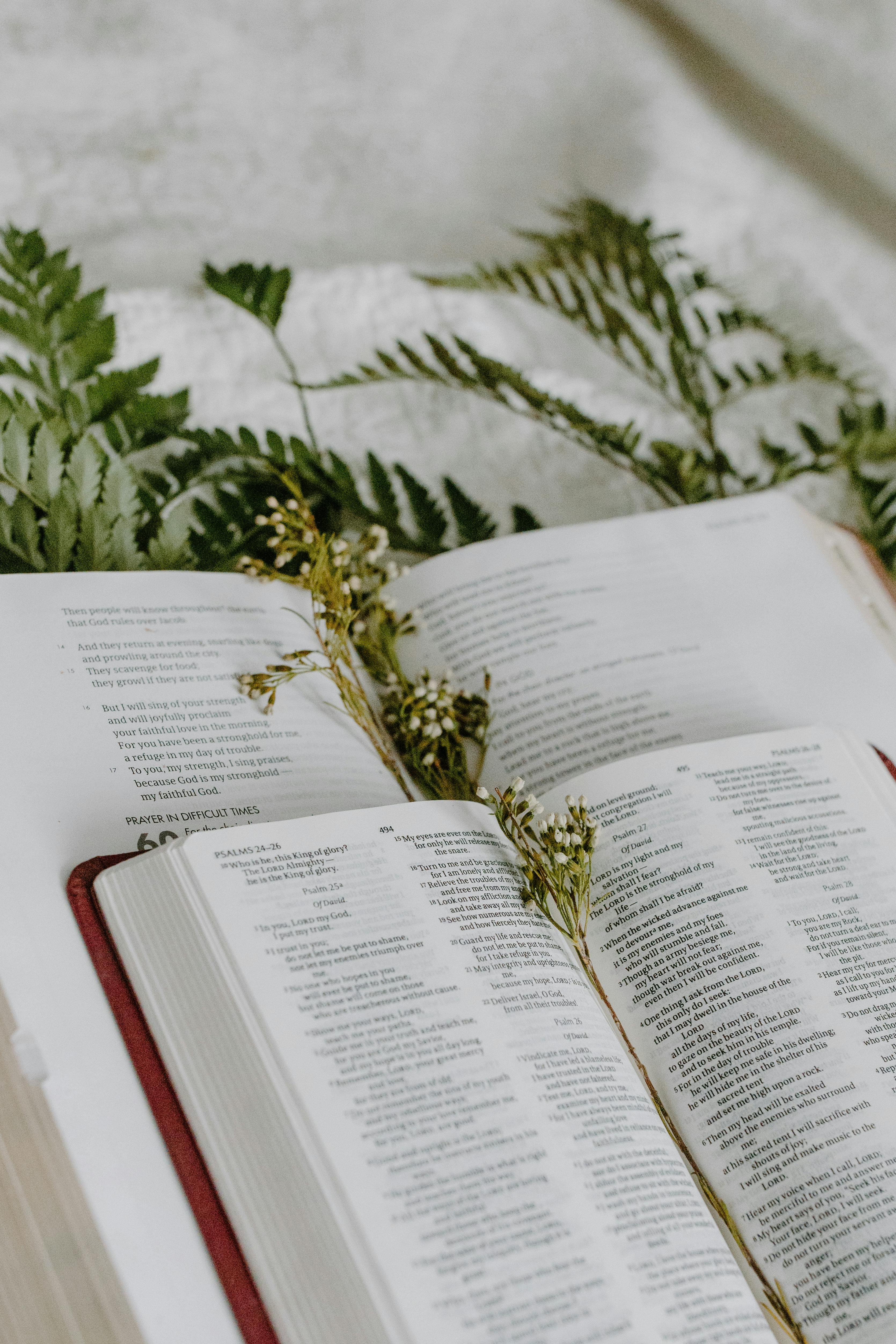
Effective Ways to Use a Torque Wrench: Essential Tips for 2025
Using a torque wrench properly is crucial for achieving accurate and safe fastening. Whether you're a seasoned mechanic or a beginner, understanding how to use this essential tool can significantly impact the durability and safety of your projects. A torque wrench ensures that the correct amount of torque is applied to fasteners, which minimizes the risk of joint failure or material damage.
This guide will explore various aspects of torque wrenches, including how to use a torque wrench, the different types available, calibration techniques, and essential safety tips. By the end of this article, you will be equipped with the knowledge to enhance your DIY projects or professional work in 2025 and beyond.
We will cover:
- Understanding torque and how it affects fasteners
- The various types of torque wrenches and their applications
- Step-by-step instructions for proper use and calibration
- Troubleshooting common issues and maintaining accuracy
- Best practices for safety and efficiency
Let's dive into the fundamentals of using a torque wrench effectively.
Understanding Torque and Its Importance
To effectively use a torque wrench, you must first grasp the concept of torque. Torque is a measure of the rotational force applied to an object, often represented in units like foot-pounds or Newton-meters. Proper torque application is critical because exceeding or not reaching the specified torque can lead to fastener failure.
What is Torque?
Torque is defined as the tendency of a force to rotate an object about an axis. It plays a key role in mechanical engineering, especially regarding how parts fit together. Understanding torque allows you to apply the right amount of force without compromising joints or materials. For example, applying too much torque to a bolt can strip the threads, rendering the connection ineffective.
How Torque Affects Fasteners
The relationship between torque and fastener tension is crucial. Insufficient torque can lead to joints loosening over time, while excessive torque increases the stress on fasteners, increasing the risk of material failure. For instance, during vehicle maintenance, proper torque application ensures each bolt and nut has the ideal tension, keeping components secure and functional.
Torque Specifications and Their Importance
Every application comes with its torque specifications, which determine the correct amount of torque to apply. These specifications can vary by material type and application. For instance, soft materials such as aluminum may require lower torque settings to avoid deformation, while harder metals can tolerate higher torque levels. Familiarizing yourself with the torque requirements will prevent potentially dangerous mechanical failures.
Types of Torque Wrenches and Their Applications
Choosing the right torque wrench is fundamental for effective torque application. There are several types of torque wrenches, each designed for specific tasks and measurements.
Manual Torque Wrenches
Manual torque wrenches are traditional tools requiring physical resistance to set the desired torque. These wrenches must be adjusted correctly to ensure accuracy. When using a manual torque wrench, it's vital to follow the manufacturer's instructions regarding torque settings and application techniques to avoid under or over-torquing.
Digital Torque Wrenches
Digital torque wrenches provide a digital display for easier reading and accuracy. They often include features like audible alerts to indicate when the desired torque setting is met. Digital models have become popular in various industries due to their precision and user-friendly interfaces, ideal for both automotive and industrial applications.
Hydraulic and Pneumatic Torque Wrenches
Hydraulic and pneumatic torque wrenches are commonly used in industrial settings, where high torque levels are necessary. These tools leverage hydraulic or pneumatic systems to provide powerful tightening capabilities, making them suitable for large equipment and high-stakes assembly tasks. The torque settings are often adjustable, offering flexibility for different materials and applications.
Step-by-Step Instructions for Proper Torque Application
Using a torque wrench might seem straightforward, but improper technique can lead to serious issues. Here’s a detailed guide to follow for effective torque application.
Preparing to Use a Torque Wrench
Start by selecting the right torque wrench for the task at hand. Then, gather necessary tools, including the correct socket size for the fastener. Always check that the torque wrench is calibrated and in good working condition before Usage.
Setting the Torque Wrench
Adjust the torque wrench according to the specifications for your project. For manual torque wrenches, turn the handle until you reach the desired setting. Digital models usually allow you to set the torque with buttons and provide a visual measurement on display. Ensure you double-check these settings to maintain measurement accuracy.
Applying Torque Correctly
When applying torque, use a smooth and steady motion, aiming to reach the torque specification indicated. Avoid jerky movements, as they can lead to inaccurate torque application. After reaching the specified torque, listen for any audible alert from a digital wrench and stop applying force immediately to prevent over-torquing.
Torque Wrench Calibration Techniques
Calibration of a torque wrench is essential to guarantee accuracy and reliability. Here, we’ll explore how to calibrate a torque wrench effectively to maintain its precision over time.
Importance of Calibration
Calibration ensures that the readings on your torque wrench correlate accurately with the real torque requirements. Regular calibration is crucial, especially for tools used frequently in critical applications, such as auto repairs or machinery assembly. Failure to calibrate can result in significant issues, including component failure and safety hazards.
How to Calibrate a Torque Wrench
Calibrating a torque wrench involves following a few essential steps. Start with an appropriate calibration tool, typically a torque calibration tool, which accurately measures the applied torque. Set the wrench to a specific torque value and use the calibration tool to measure the actual result. Adjust the wrench settings accordingly until the readings align correctly. Repeat this process for multiple settings to ensure comprehensive accuracy.
Common Calibration Mistakes
One common mistake during calibration is failing to perform checks at all torque ranges. Always test multiple points and not just a single measure to ensure broad accuracy. Additionally, neglecting periodic maintenance can also negatively affect torque wrench performance.
Maintaining Your Torque Wrench: Best Practices
Ensuring the longevity and accuracy of your torque wrench requires proper maintenance. Here are essential maintenance tips to keep your wrench in optimal condition.
Regular Inspection and Cleaning
Regularly inspect your torque wrench for any signs of wear, damage, or inaccuracies. Clean the tool after each use to remove dirt or debris that may hinder performance. Store it in a protective case to prevent accidental damage and keep it secure.
How to Store Your Torque Wrench
The way you store your torque wrench can significantly affect its lifespan. Always return the torque setting to the lowest setting to relieve tension on the internal mechanism, helping preserve its calibration over time. Store the wrench in a dry and clean area, preferably in a dedicated tool chest or holder.
Professional Maintenance Tips
If you rely heavily on your torque wrench, consider sending it for professional calibration and maintenance regularly. This ensures that it remains in top operating condition, ready to deliver accurate torque measurements every time.
Torque Wrench Safety and Troubleshooting
Using a torque wrench safely is as important as understanding its function. Follow these safety tips to prevent accidents and ensure effective usage.
Torque Wrench Safety Tips
Always wear appropriate safety gear, such as safety goggles and gloves, when operating a torque wrench. Additionally, ensure you are using the correct measurements and setting to prevent potential injuries from fasteners failing. Regularly review safety guidelines provided by the torque wrench manufacturer for best practices.
Common Torque Wrench Issues
Common issues include incorrect readings and the inability to adjust settings accurately. If you encounter problems, it may signal that the wrench needs calibration or repair. Always consult the user manual for troubleshooting tips from the manufacturer, and if necessary, address any issues promptly to maintain tool performance.
Final Recommendations for Successful Torque Application
To achieve the best results with your torque wrench, stay well-informed of torque specifications available for your projects. Keep your torque wrench well-maintained, routinely calibrated, and educated about its safety features to enhance effectiveness. By following these essential tips, you'll not only ensure accurate torque application but also contribute to safe and successful project outcomes.
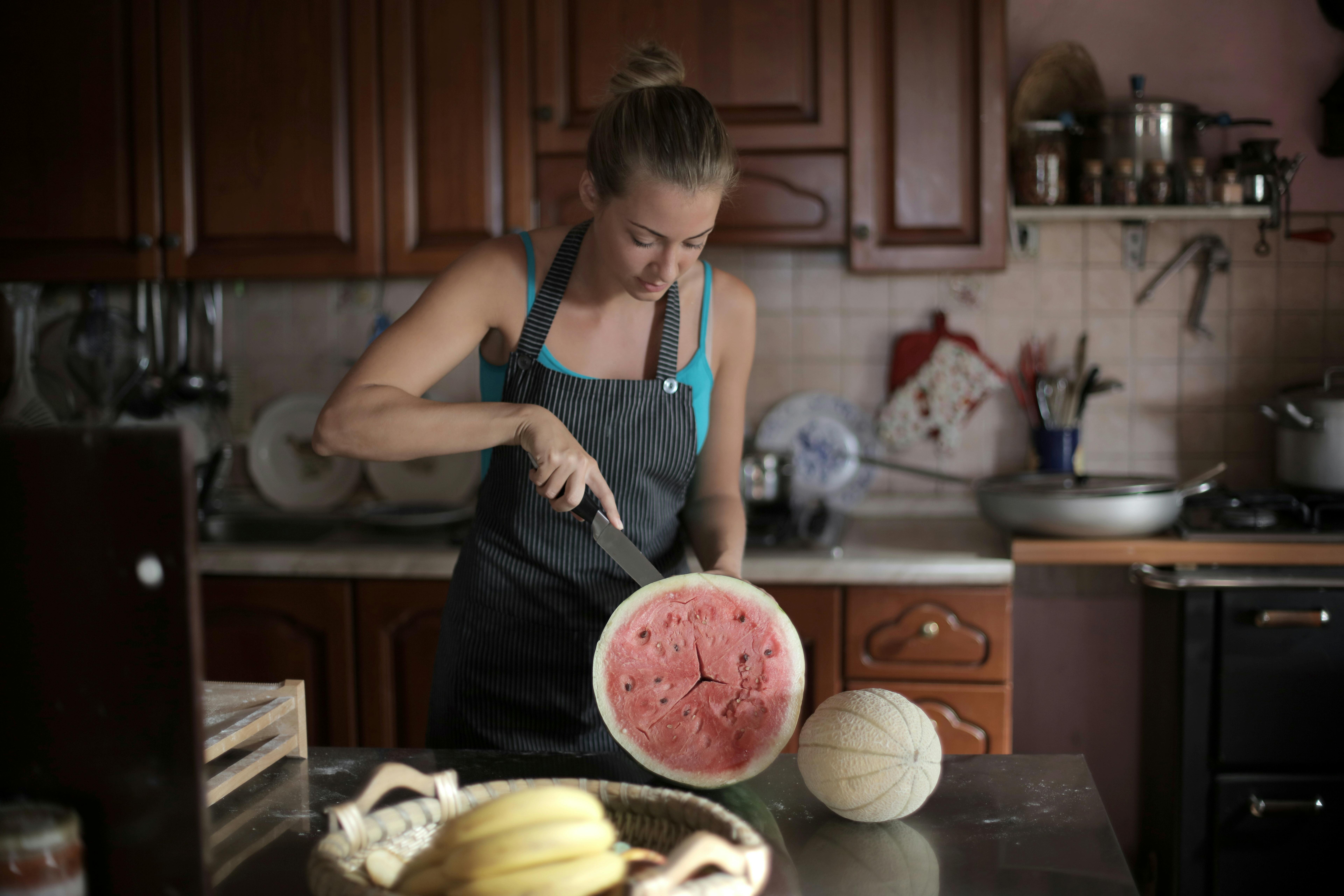
